PVD Coating
Ever noticed how some items sparkle and gleam, catching your eye from across the room? Well, chances are, PVD coating had something to do with it! This process gives objects that extra pop of color and shine, turning ordinary into extraordinary. So next time you admire something glossy, remember, it’s the magic of PVD which you want to bring into your home or office.

PVD Coating Process
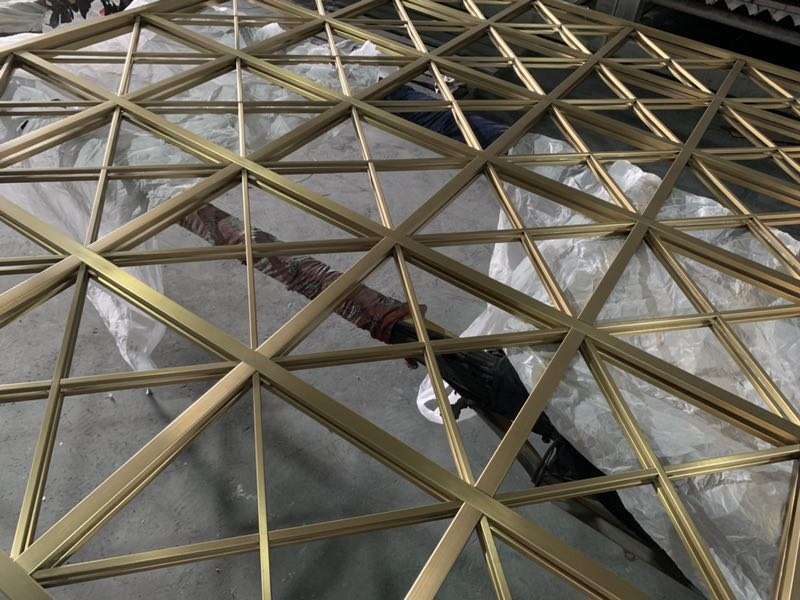
Preparation of Substrate: Before the deposition process begins, the substrate material (the material to be coated) is cleaned thoroughly to remove any contaminants or oxides from its surface. This ensures proper adhesion of the coating.
Vacuum Chamber: The substrate and the material to be deposited (often referred to as the target) are placed inside a vacuum chamber. The chamber is evacuated to create a vacuum environment to prevent unwanted reactions and contamination during the deposition process.
Heating the Target: The target material, typically a metal or a compound, is heated to a high temperature, causing it to vaporize. This vaporization can occur through various methods such as resistive heating, electron beam heating, or sputtering.
Deposition Process (Sputtering):
In sputtering, inert gas ions (such as argon) are introduced into the vacuum chamber. These ions strike the target material, dislodging atoms or molecules from its surface. These ejected particles then travel in straight lines and deposit onto the substrate, forming a thin film.
Film Characteristics: The properties of the deposited film depend on several factors, including the composition of the target material, the deposition parameters, and any post-deposition treatments. PVD coatings can exhibit properties such as high hardness, wear resistance, corrosion resistance, low friction, and high-temperature stability.
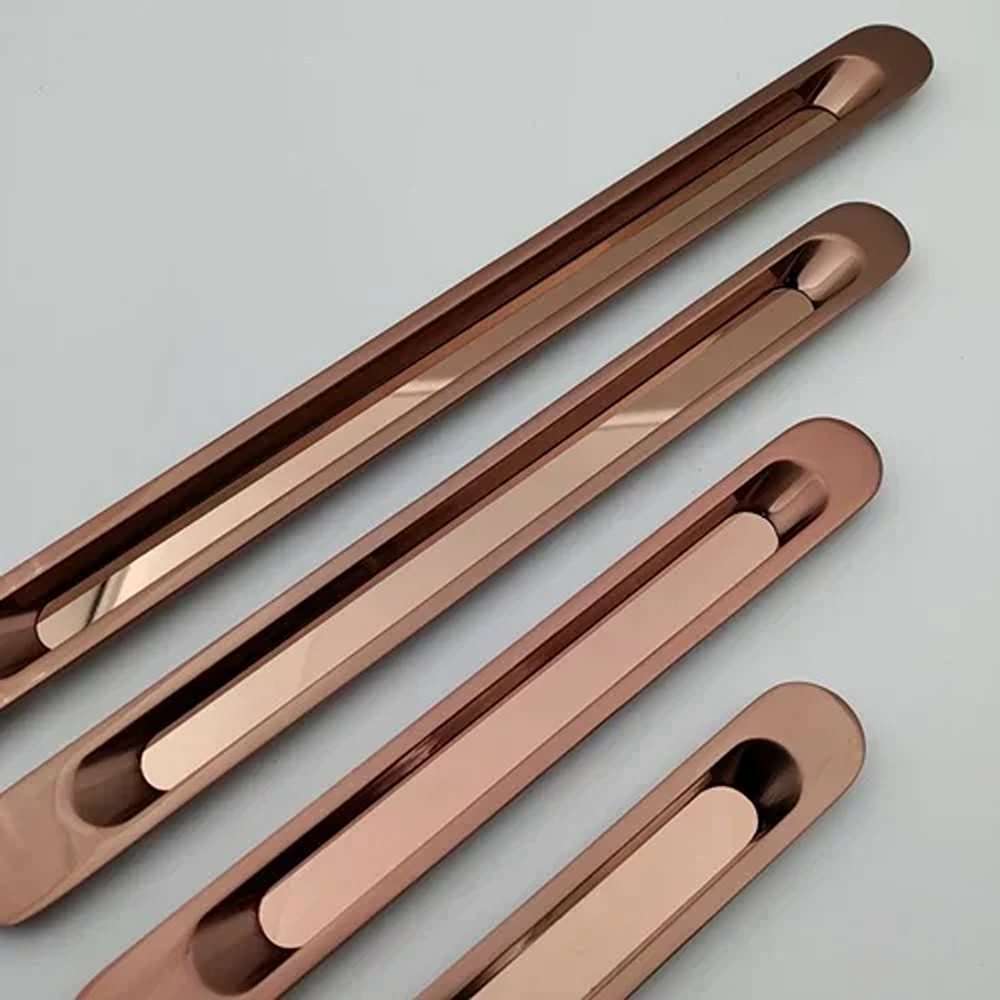
Advantages of PVD Coating

Enhanced Aesthetic Appeal
PVD coatings can provide stainless steel surfaces with a wide range of colors and finishes, including gold, bronze, black, and gunmetal. This allows for customization and aesthetic enhancement, making stainless steel products more visually appealing and suitable for various design requirements.
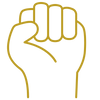
Improved Durability
PVD coatings significantly increase the hardness and scratch resistance of stainless steel surfaces, making them more durable and resistant to wear and tear. This is particularly beneficial for applications where stainless steel products are subjected to harsh conditions or frequent handling.

Increased Corrosion Resistance
PVD coatings act as a protective barrier against corrosion, enhancing the inherent corrosion resistance of stainless steel. This makes coated stainless steel products suitable for use in corrosive environments, such as marine or outdoor applications.
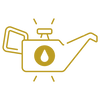
Easy Maintenance
PVD-coated stainless steel surfaces are easy to clean and maintain, as the smooth, non-porous coating prevents dirt, oil, and other contaminants from adhering to the surface. This simplifies maintenance and prolongs the lifespan of coated stainless steel products.

Temperature and Chemical Resistance
PVD coatings on stainless steel surfaces can withstand high temperatures and resist chemical exposure, making them suitable for use in demanding applications such as automotive, aerospace, and industrial equipment.

Environmentally Friendly
PVD coating processes are environmentally friendly, as they typically involve the deposition of thin films in a vacuum environment without the use of hazardous chemicals. This reduces waste and minimizes environmental impact compared to traditional plating methods.
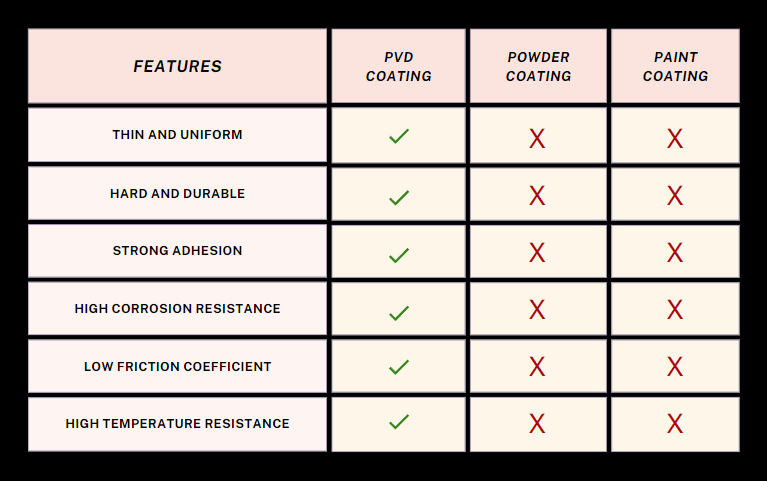